Industrial Heating Systems
Industrial heating processes can be broadly categorized as low-temperature (to about 400 °C or 752 °F), medium-temperature (between 400 and 1,150 °C or 752 and 2,102 °F), and high-temperature (beyond 1,150 °C or 2,102 °F). Low-temperature processes include baking and drying, curing finishes, soldering, molding, and shaping plastics. Medium temperature processes include melting plastics and some non-metals for casting or reshaping, as well as annealing, stress-relieving, and heat-treating metals. High-temperature processes include steelmaking, brazing, welding, casting metals, cutting, smelting, and the preparation of some chemicals.
Batch ovens are furnaces built for thermal processing including drying, curing, and baking. THERMOCOAT industrial batch ovens are designed to meet the strict requirements of the variety of product range. The heating source varies according to product requirements. These mainly include electrical batch ovens, Infrared batch ovens, microwave batch ovens, Steam batch ovens, Gas fired ovens. View our line of Industrial Batch Ovens.
Curing with Infrared and Combination Ovens
IR curing systems are helping manufacturers increase productivity. IR-enhanced convection systems combine the process-friendly characteristics of convection with the speed of IR.
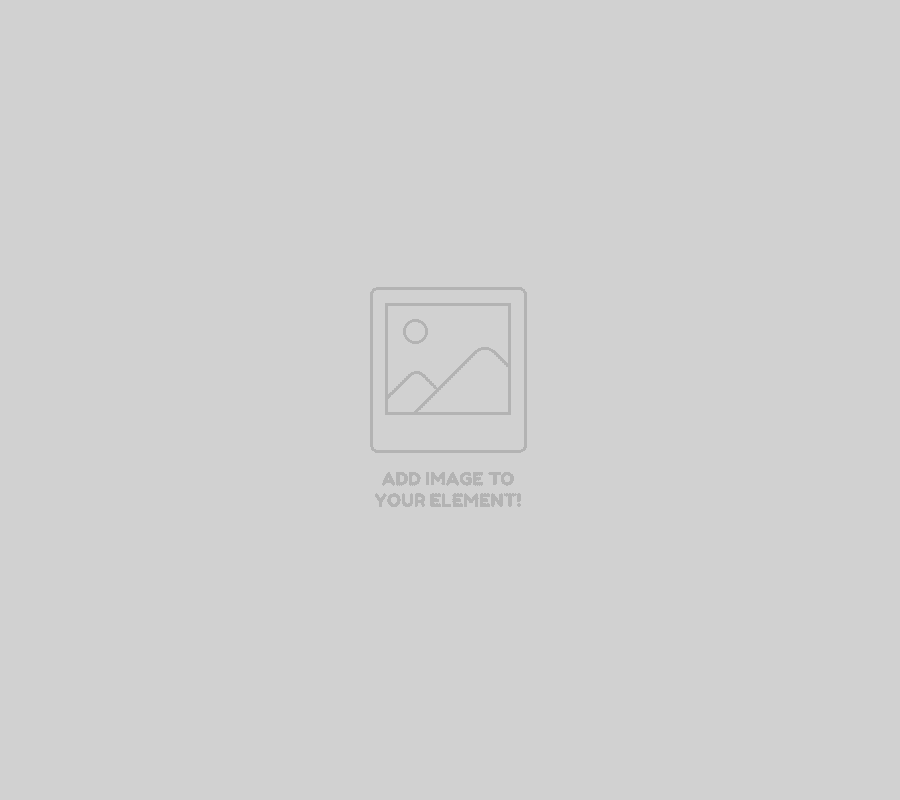
Figure 1: Stringent environmental regulations and competitive pressures that demand higher quality and improved productivity-faster cycle times, automated operations and just-in-time delivery-have led industrial finishers to consider alternatives to conventional heating systems. In a growing number of applications, manufacturers are also turning to infrared-enhanced convection oven systems to preheat, dry, and cure applications.
Principles of IR
All bodies (at temperatures above absolute zero) naturally emit and absorb energy as electromagnetic waves. When a material absorbs electromagnetic energy, changes take place within the molecules. Depending on the radiation wavelength, these changes may involve electron-orbiting levels, bonds connecting atoms, or the nuclei of the atoms themselves.
There are three methods by which heat can be transferred from one body to another: conduction, convection, and radiate.IR waves and microwaves are both in the electromagnetic spectrum, which also includes radio waves, ultraviolet radiation, X-rays, and visible light. The different categories of electromagnetic energy are classified by wavelength, which is the distance between radiation energy pulses (Figure 1).
Within the IR spectrum, wavelengths are divided into three bands:
- Short Wave, which overlaps the end of the visible light spectrum (0.76 to 2.3 microns)
- Medium Wave (2.3 to 3.3 microns)
- Long Wave (3.3 to 1,000 microns)
Trace levels of long-wavelength IR energy are emitted from most substances at room temperature. As a body warms, however, it begins to radiate increased amounts of IR energy at reduced wavelengths. When the temperature reaches approximately 1,100ºF, the emitting energy reaches the medium-wavelength IR range. Increasing the temperature even further produces short-wavelength IR energy.
When IR energy is absorbed, the bonds that join atoms within the molecule are affected. Normally the bonds vibrate with consistent amplitude. However, the amplitude increases with the absorption of energy and then returns to normal. The molecule returning to its low-energy state releases the energy as heat. It is this heating that preheats, dries, or cures a coating.
Some of the IR waves intercepting a body are absorbed and converted to heat. The rest either pass through the material or are reflected back toward the energy source. If a molecule absorbed all IR energy equally, the application of IR technology would be relatively simple. However, a given type of molecule will absorb a certain wavelength of IR energy more readily than others. At some wavelengths, a large percentage of photons are absorbed while at other wavelengths, no energy may be absorbed.
The type of molecular bonds contained in a material and the vibrations they undergo determine which wavelengths of energy will be absorbed, as well as the relative strength of the absorption. Consequently, the IR-absorption characteristics of coatings tend to vary with their chemical makeup.
Principles of Convection Curing
Convection oven systems use moving air as the medium for heat transfer. This method of energy transfer is acceptable for a slow cure but does not lend itself to accelerated cure times if high quality is to be maintained. While a wide range of temperatures and airspeeds are theoretically possible with the precise control over an accelerated curing process. Cure times may be lowered by increasing temperature and/or the velocity of air within the oven.
Typical low-velocity convection ovens have airspeeds of 200 fpm, while high-velocity nozzles produce nominal air speeds of up to 3,000 fpm. When high airspeeds are employed to reduce cure time. Compared to IR energy, convection curing does enjoy some advantages in some specific applications. Unlike IR, which requires line-of-sight transmission of energy to surfaces, the use of circulating air allows heat to reach areas such as interiors of 3-D shapes that are hidden from direct exposure and enables the oven to maintain all surfaces at a constant temperature.
In addition, while the convection-energy transfer is slower than IR, it is more forgiving for heating substrates that vary in mass and/or thickness, such as irregular shapes. With IR-energy transfer, the longer an object is exposed, the hotter the thinner sections become due to low mass-to-surface-area ratios
Thus, IR-enhanced convection combines the best properties of infrared and convection oven systems and produces high-quality curing and coating in significantly less time than is possible using convection methods alone. In addition, IR-enhanced convection produces more process-friendly characteristics than are possible with IR alone. IR-enhanced convection involves more variables but more opportunities for fine-tuning the cure.
THERMOCOAT offers energy-efficient custom infrared ovens used for stationary batch processes. Some applications include mold pre-heating, glue activating, drying, fusing, annealing, and curing. Product temperatures of 150 degrees F to 600 degrees F are common for Infrared Batch Ovens, while higher temperatures can be achieved.
For the oven heat source, THERMOCOAT offers a variety of environmentally-friendly electric infrared heaters, each with its own heating advantages and unique characteristics. All heaters are completely manufactured at THERMOCOAT, assuring you the highest quality, proper application, and continued support. Along with infrared heat, we can include re-circulated or heated air input for a combination infrared/air oven.
A reliable custom control panel can be supplied for the oven with optional timers, precise solid-state controllers, and sensors as required. We also offer custom carts or racks to transfer or hold your products.
All batch ovens are completely factory assembled, set up, and tested prior to shipment to assure a simple trouble-free start-up.
Advantages
- Highly efficient in converting electrical energy into heat for electrical IR.
- Greater rate of heat transfer.
- Compact in size.
- Heats only the object without heating the environment.
- Easy to zone for uniform heating of the product.
- Faster response to changing process conditions.
- Quick start-up and shut down.
- Easy to have cut-off zones for narrow widths.
- Easy to control and automate.
- Lower capital and installation cost.
- Can be easily be added to existing conventional dryers to increase line speed.
- Infrared Air dryers suitable for solvent-based coatings.
Application of Infrared Dryers
- Drying of Fruits and Vegetables.
- Drying of ink and paper.
- Drying of coats in Coating line.
- Dry and Pre-dry Water and Solvent based Pressure Sensitive Adhesives.
- Laminate foam to fabric using web adhesives for automotive and furniture industries.
- Drying of water-based latex and clay coatings on paper.
- Preheat films for laminating and embossing.
- Drying of fabrics in Textile.
- Cure Silicone coatings on various substrates.
- Dry and cure solvent base resin coatings for the electronics industry.
- Cure 100% solids resin coatings on fiberglass for Printed Circuit Boards.
- Drying and curing coatings on industrial fabrics.
- Drying of pharmaceutical coating.
- Max belt Speed: 15 Mtr/ Min.
- Sterilization of packaging containers for food and pharmaceutical industries.